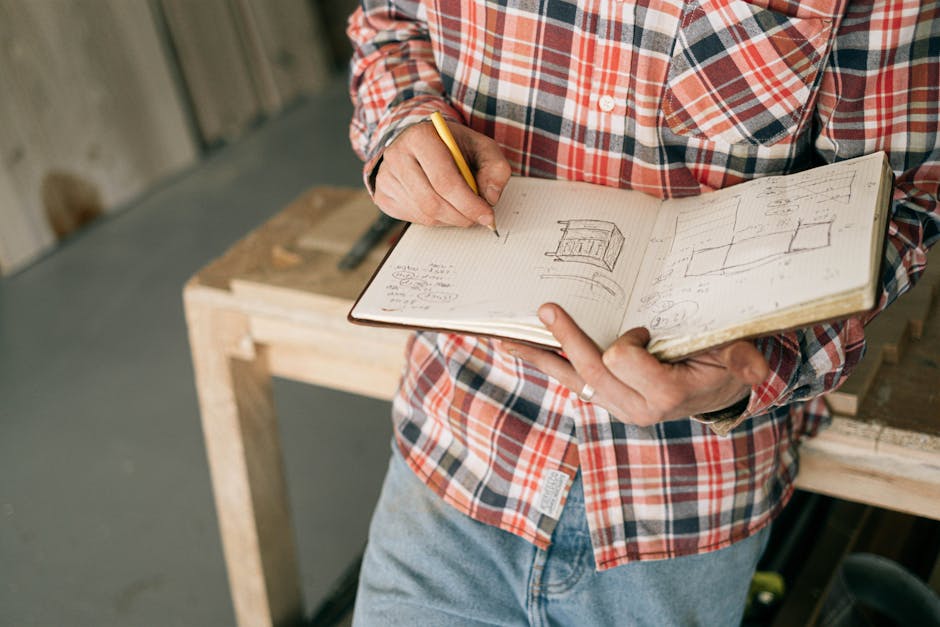
Lean Manufacturing - Increase Efficiency and Reduce Waste
Lean Manufacturing - Increase Efficiency and Reduce Waste
Lean manufacturing is a systematic approach aimed at increasing efficiency while reducing waste in the manufacturing process. By implementing lean principles and practices, businesses can improve productivity, cut costs, and deliver higher quality products to customers.
Key Principles of Lean Manufacturing
- Continuous Improvement: Lean manufacturing encourages an ongoing effort to identify and eliminate waste, improve processes, and optimize workflow.
- Just-in-Time Production: The goal is to produce and deliver products in the exact quantity and at the precise time they are needed, reducing inventory and minimizing storage costs.
- Respect for People: Lean manufacturing values the involvement and contribution of employees at all levels, fostering a culture of collaboration, empowerment, and innovation.
Strategies for Implementing Lean Practices
- Value Stream Mapping: Analyze and visualize the flow of materials, information, and activities to identify areas of waste and opportunities for improvement.
- Kaizen Events: Rapid improvement events focused on solving specific problems or implementing small-scale process changes.
- 5S Methodology: Sort, Set in Order, Shine, Standardize, and Sustain - a system for organizing the workplace to improve efficiency, safety, and productivity.
- Kanban System: A visual signaling system that helps manage inventory levels and ensure a smooth workflow.
- Poka-Yoke: Error-proofing mechanisms and techniques to prevent defects or mistakes from occurring in the manufacturing process.
Implementing lean manufacturing requires a commitment to embracing change and continuously striving for improvement. By eliminating waste, streamlining processes, and fostering a culture of collaboration, businesses can achieve substantial increases in efficiency, productivity, and overall success.